My dad had the idea of drilling the holes way larger so we could slide an alternator bushing inside the hole. Then we would weld it real good and grind it flat on the inside. We tried it and it seems to work so far.
The bushing from an alternator my dad had in a pile of nuts and bolts.
The trac bar holes drilled out to the outside diameter of the bushing (actually in our case filed out since someone bought a drill bit but didn't have a 1/2" drill to use it.)
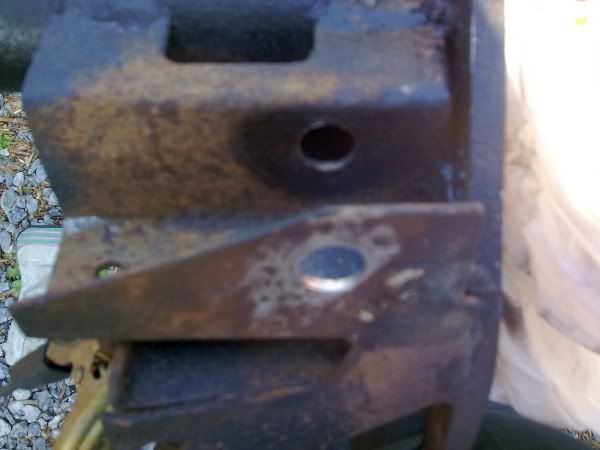
Cut the bushing in half so that we could use it for both holes. Then we placed it in place inside the holes and used my new 7/16" bolt through them to hold them in place for tac welding.
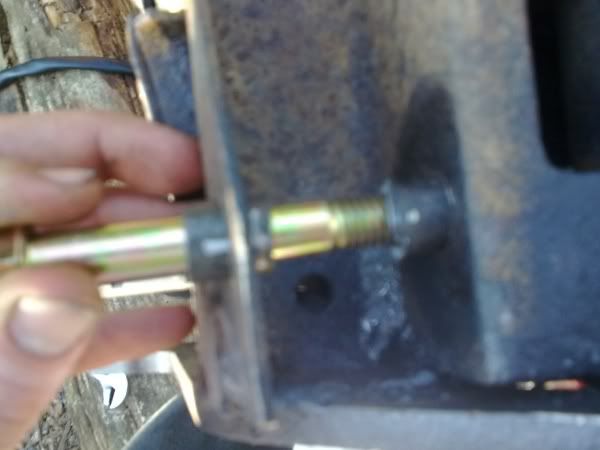
The inside hole welded and ground down, getting ready to do the outside hole.
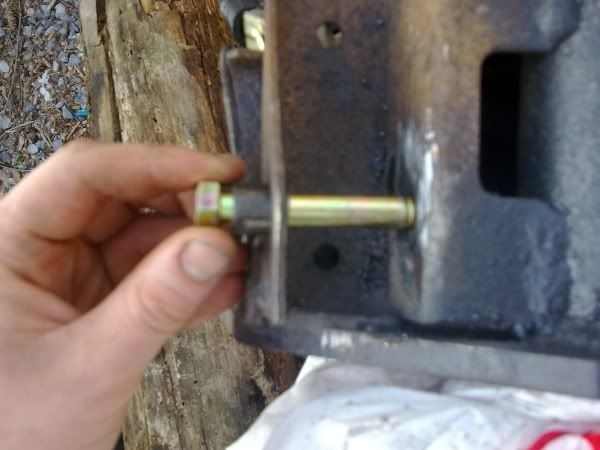
We made the front one stick out about a 1/4". So instead of having it just go into two pieces of sheet metal basically we built it up so hopefully if something starts to vibrate it won't egg the tunnel out as easy. Then we ground it down so the washer and bolt head had a flat spot to rest on and painted it.
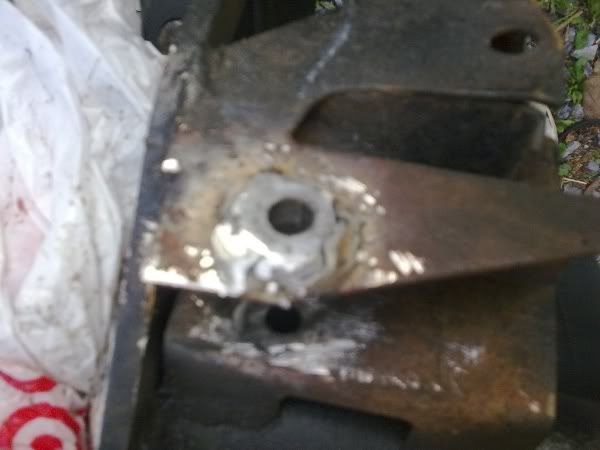
Since the original bolt was 3/8" and the bushing inside my trac bar was 7/16" I got a new grade 8 7/16" bolt and nut to use so everything was a slight bit tighter. I just took the original 3/8" nut out of the little bracket and we welded my new nut to it. Also, the inside diameter of the alternator bushing was a slight bit smaller than 7/16" so we just drilled it out a slight bit.
P.S. They say a picture is worth 1,000 words but mine are from a cell so they are pretty much worth 1,000 drunken slurred words